Stanley Electric’s Manufacturing
Toward the goal of achieving a “manufacturing structure that manufactures only the number of products customers need when customers demand them,” the entire Stanley Group practices “SNAP,” which is generic name for the company’s own production innovation activities. By thoroughly cutting down on wastefulness, we shorten lead times, reduce costs, improve quality, and meet delivery deadlines, thereby enhancing customer trust and satisfaction. Indirect departments are also thorough in their pursuit of work efficiency, and they also promote production engineering improvements through the inhouse production of equipment and research into new materials.
What is SNAP?
SNAP stands for Stanley New Approach for higher Productivity, which is a generic name for the Stanley Group’s style of production innovation activities. The objectives of the activities are (1) offer value that satisfies customers (QCD) and (2) become a competitive company capable of producing profit in any environment through companywide cost reductions achieved by the thorough elimination of wastefulness.
Starting in 1997 with guidance from external consultants, a department was established to lead SNAP for the entire company. SNAP has promoted education and activities mainly in the production environment where “wasteful movement and transport” and “wasteful stagnation” are defined as the two major types of wastefulness. In the early stage of introduction, selected production employees, who were sent to training sessions organized by external consultants to understand the gist of SNAP and acquire know-how, rolled out the SNAP activities, whereas currently, training is provided to all employees with inhouse coaches to ensure that SNAP spreads through the company, and at the same time the company is promoting companywide activities and work efficiency not only within the confines of the production environment.
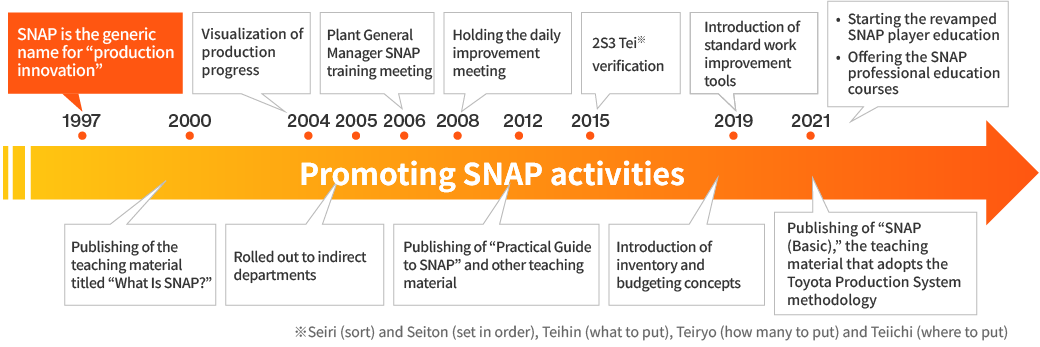
Organizational structure and educational structure
We advance improved cooperation with the “companywide cross-functional department” based at Hadano Factory, where companywide SNAP activities are centrally organized and SNAP education and improvement techniques are standardized, and with the “promotion department” placed at each factory. The “companywide cross-functional department” is staffed with regular salaried employees and employees reassigned from other departments or related companies inside Japan through internal job rotation. The employees reassigned to the “companywide cross-functional department” work on improvements at other factories and acquire knowledge for two years, and are then assigned back to serve the roll of promoting SNAP at their own departments.
The internal certificates for SNAP are offered for three levels: “SNAP Players,” “SNAP Trainers” and “SNAP Professionals.” Training is provided according to each curriculum, and employees are awarded a certificate upon completion of their training. In the training, employees are trained to get the knack of identifying wastefulness in the actual production environment and learn improvement techniques. In order to roll out SNAP to the entire company not limited to only the production environment and also to get all employees involved in daily improvements based on the knowledge and skills of SNAP, the possession of the “SNAP Players” certificate is reflected in the human resources system as a condition for obtaining a promotion to encourage all employees to obtain the certification.
Moreover, the “SNAP promotion meeting” is held once a year as the place for reporting and mutual communication on SNAP activities, where the management and production bases in Japan and outside Japan get together online to present examples of improvements with thorough elimination of wastefulness, share know-how, ask questions, and seek advice. We endeavor to activate companywide SNAP activities to lead to cost reductions as One Stanley.
-
SNAP promotion meeting -
Player training
SNAP2 project
In the phase VIII mid-term three-year business plan from April 2023, we have added “SNAP2” as new activities for maximizing gross profit, which is the source of profit. In order to provide quality products while facing declining selling prices in line with the automobile industry market where EVs are increasingly adopted, we are working on cost reduction activities as an integral whole with suppliers by way of “SNAP2,” which reviews materials to place priority on “material cost reduction” and “shift to inhouse production” in addition to cutting down on expenses with the elimination of wasteful production processes, which has been the core of activities. Regarding the shift to inhouse production, which is based on our determination regarding how much gross profit can be secured from an investment, we enhance production efficiency by increasing the utilization rates of facilities from the perspective of fully utilizing all facilities owned by globally-based factories instead of overseeing on a factory basis.
With this addition of new activities for evolving the production innovation activities, the Group refines the cost reduction strategy as a competitive advantage.